Telescopic springs are manufactured from high quality strap iron, according to the ISO 9001. They are used for covering a spindle and a ball screw. It is possible to assemble the springs without removal a ball screw.
New generation of high-performance telescopic springs:
- Among various shapes of spindle covers telescopic springs continue to hold an important role.
- Telescopic springs are made using special machines that are permanently adjusted to the customers’ requirements.
- Telescopic springs are introduced on the marked as protective covers of spindles already for a long time.
- They are successfully presented on the market as indestructible, precise, and in various dimensions.
- The new standard program now includes about 1,500 types of springs in dimensions from 15 mm up to 230 mm of internal diameter.
- The extension length is up to 4,500 mm with vertical types.
- Another production variant is stainless steel springs
- Telescopic springs are made in a standard design of blue steel.
Technical Data
Spring strip steel of extreme hardness is used for standard telescopic springs (55-58 Rockwell) and strength of up 1,800 N/m2. Thickness of the strip steel is from 0.2 to 1.0 mm. If the telescopic springs are regularly exposed to effects of cooling liquid with high water ratio, it is suitable to use telescopic spring of stainless steel. Stainless steel telescopic springs show limited spring forces so they cannot be made in all sizes. Optimum operating conditions are while using in oil (greasy) environment. With minor particles and dust composed bags are alternatively used. Telescopic springs are used for speeds up to 40 m/min as standard.
Maintenance and Cleaning
Maintenance of spiral springs is unnecessary. We recommend cleaning according to the rate of pollution and then apply oil film.
Assembly and operating time
Telescopic springs have different extension according to the assembly position.
I. Horizontal position – Horizontally assembled springs are used with especially even operation while the overlap of individual threads will be larger. This means that the sag, especially with springs with a large extensive length, will be decreased and the lateral stability of springs will be improved. With horizontal use it is recommended to orient the spring so that the splinters fly from the largest diameter of the spring to the smallest diameter of the spring.
II. Vertical position – With vertical use of the springs it is possible to achieve significantly larger extensive length than with the horizontal use. Vertical springs have a high extensive force that secures perfect operation of the spring. We recommend placing the larger diameter of the spring into the upper flange for vertical use.
Flanges
Simple centring flanges are needed for assembly of telescopic springs on both ends. The flanges must allow for free movement of the spring so that jamming of the spring in the flange does not occur. The spring rotates in the flange during compression and extension. The springs must not be riveted, screwed or otherwise fixed to the flange.
Gallery
Downloads


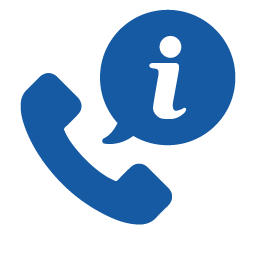
We look after our customers with utmost care. If you have a question, suggestion, or comment, please do not hesitate to contact us.